You Need to Get a Grip on End-of-Arm Tooling
We might think manufacturing happens in the background, but that’s the wrong perspective. From another point of view, manufacturing supply chains and support infrastructure are central to modern living.
Manufacturing finds itself the center of an engineering revolution thanks to robots and automation. Robotics is especially consequential today given the number of industrial positions going unfilled and companies looking for a competitive edge amid globalization.
Collaborative robots (cobots) and automated robotic arms can have different tool types depending on the application and the desired outcome. One differentiation worth knowing about is pneumatic versus electric end-of-arm tooling (EOAT). These are the tools at the end of the arm the robot manipulates to interact with materials and workpieces.
Why Does It Matter?
Robotics is hardly a dry subject — but it might take some convincing for you to care about end-of-arm tools unless you’re in the robotics, manufacturing or automation industry already.
Suffice it to say, modern industrial robots couldn’t do any of their lifting, carrying, turning, cutting, engraving, measuring, testing or dozens of other tasks without end-of-arm tools.
Typical examples of end-of-arm tooling implements include:
- Welders
- Grippers
- Laser cutters
- Measurement tools
- Material removal tools
- Collision and force-torque sensors
- Suction cup or electromagnetic lifters
In addition to tools that cut, grind or polish, robot arms may also use EOATs to perform testing, calibrations or inspections. EOATs give robots the ability to do the tasks we require of them, and they support an ever-larger selection of robotics platforms and applications.
Below, we’ll look in more detail at the upsides and downsides of pneumatic and electric EOATs.
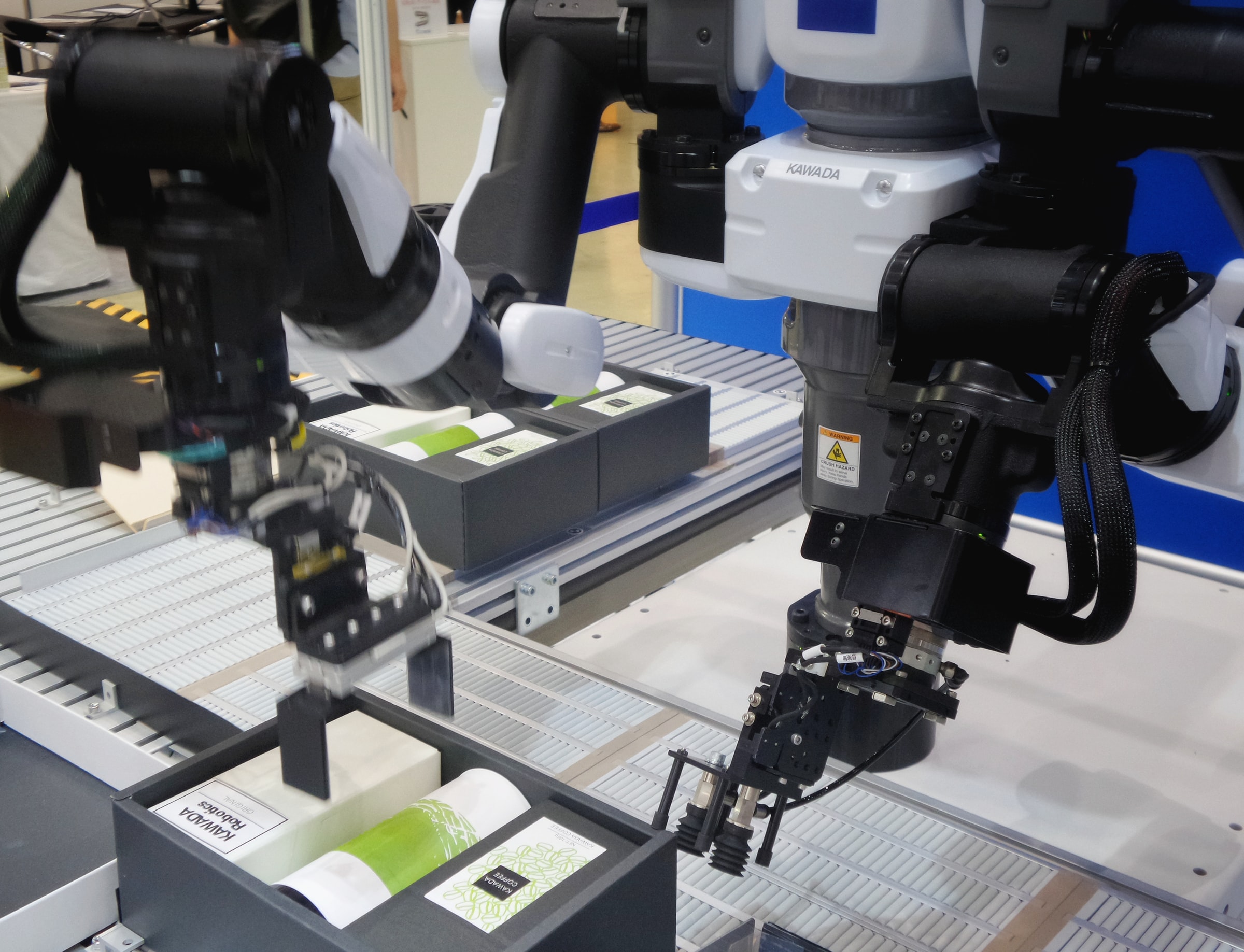
Pneumatic EOATs: Advantages and Disadvantages
Without the right kind of end-of-arm tooling, an industrial robot can’t complete the task set before it. There are just as many concerns from the business side of things.
First up is pneumatic. Pneumatic EOATs are the top choice among robotics engineers. Yet what are the specific advantages? For one, pneumatic EOATs have a high power-to-size ratio compared to other options. As a result, they can be easier to fit into certain robot chassis or industrial work areas. Companies concerned with startup costs may also fare better with more familiar pneumatic actuators and EOATs. There’s more to the equation, but day-one costs are easier to manage with pneumatic EOATs.
Pneumatic operation is ideal for high-efficiency setups, where the shape and size of workpieces do not change frequently. Many pneumatic EOATs can tool or manipulate one type of part only.
Nevertheless, pneumatic EOATs aren’t without their disadvantages. They’re the top choice right now, but they have clear drawbacks that may see them retired from factory floors in the coming years in favor of their electric counterparts.
These disadvantages are easier to work around in some situations, but they’re still worth noting as companies ponder this choice:
- Less advanced programmability: Compared to electric EOATs, which are more programmable for flexibility, pneumatic grippers and other end-of-arm air tools provide simple open-close functionality.
- Limited control over grip force: Electric EOAT grip force is far more customizable, although pneumatic variants may allow rudimentary grip control by varying the pressure.
- Require access to compressed air: EOATs require continuous access to compressed air, which adds to their ongoing operational costs.
- Can compromise quality due to lubricants: The contaminants within compressed air systems may pose a threat to some especially vulnerable products, like foods, depending on the application.
Electric EOATs: Advantages and Disadvantages
Engineering circles increasingly look to electric end-of-arm tools as the logical replacement for pneumatic robotic arm tools. Although they can serve many of the same functions, electric actuators and EOATs are substantially more flexible in some key ways.
Here are the advantages of electric end-of-arm tools:
- Greater programmability and control: Electric EOATs provide the user with significant — and programmable — control over positioning, tool force, travel distance and travel velocity. These features are essential when material, product or part sizes change regularly.
- Simple system and setup: Using electric EOATs delivers the benefit of eliminating an air compressor and its associated maintenance and replacement cycles. The relative simplicity of electric actuators and EOATs is attractive for outfits with limited engineering personnel.
- Easier to control at lower pressures: As mentioned, air-based tools offer basic pressure control only. At lower pressures, it’s extremely difficult to obtain a useful amount of force from the tool. Electric variants eliminate this shortcoming by providing gripping power even during delicate operations.
- Less strict space requirements: Because pneumatic controls are either entirely on or off at any given time, they tend to require more of a space buffer, for safety’s sake, while working with smaller parts.
One of the few disadvantages of electric EOATs like grippers is that, as discussed, they’re typically more expensive than pneumatic analogs. Pneumatic components can be cheaper on day one, but their operational costs, including compressed air supplies, eat into ROI. In comparison, electric EOATs can be costlier on day one but more affordable to maintain.
This cost-benefit trade-off of going electric is something to consider for companies looking to invest — or reinvest — in industrial robots.
Choosing Electric and Pneumatic End-of-Arm Tools
There are other ways in which your intended application influences your choice of end-of-tool arms. For example, fewer pneumatic grippers and air tools come already equipped with grip detection sensors. Electric EOATs can be easier to incorporate into a company’s growing IoT (Internet of Things) infrastructure for data-gathering purposes.
Ultimately, electric actuators and tools will probably prove the more scalable choice for the distributed, high-mix, high-volume and reasonably-priced manufacturing apparatus of the leaner, greener future.
Megan R. Nichols is a technical writer and blogger. She writes about engineering, science and technology topics. Megan is also editor of Schooled By Science, an easy to understand science blog. With Schooled By Science she hopes to encourage others to learn more about STEM subjects. Follow her on Twitter, LinkedIn or YouTube.